With the advancement of medical technology, the integration of computerization has significantly influenced diagnostic and treatment practices. One crucial component driving this transformation is the development of medical device PCBs. Specifically, medical device PCB design utilizes a variety of techniques to ensure the reliability and safety of medical devices. Incorporating standards, good design practices, and other technical features ensures that medical products are both reliable and accurate. As the trend in medical devices shifts towards creating smaller products with even greater component density, it is important to know what considerations, design tips, challenges, and manufacturing standards have the most impact on your medical device PCB design.
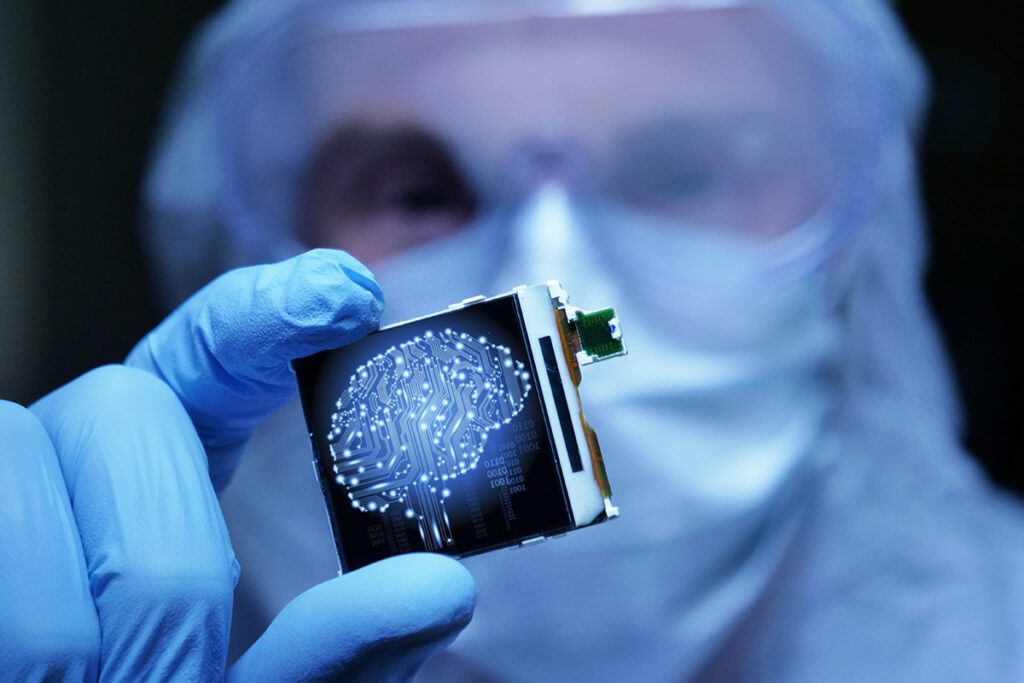
Medical Device PCB design is a nuanced topic with many contributing factors.